
The 3D printed house at 217 Carnation St. has three bedrooms and two bathrooms in 1,550 square feet of space. (Filip De Mott photos)
A homebuilding experiment more than a year in the making helped first-time buyer Tiffany Terrell finally break through the competitive local housing market.
After a six-month search and a string of four failed bids, Terrell will soon close on a first-of-its-kind property in South Richmond: the region’s first 3D-printed house at 217 Carnation St.
With construction completed over a week ago and the deal set to close next month, Terrell, 38, will pay $235,000 to purchase the three-bedroom home from the project’s investment group, which includes local housing nonprofits Project:HOMES and Better Housing Coalition, along with Virginia Tech’s Virginia Center for Housing Research.
The idea to 3D print a house came about as a proof-of-concept in the ongoing effort to make living more affordable in the state.
Virginia Housing, formerly known as the Virginia Housing Development Authority, started looking into the practice in 2019. The group awarded a $500,000 grant to the Virginia Center for Housing Research, an organization that championed the embrace of technology as one viable solution to housing affordability.
“We did more studies of this house than you’ll ever see for a 1,550-square-foot house,” VCHR Director Andrew McCoy said. He added that the agency spent a lot of time focused on the energy efficiency of the space.
The recently completed structure, which includes two bathrooms and a sizable yard, now stands out from the rest of the street. A remnant of the building process, its outside surface is a stratified pattern of wavy cement.
The home is furnished with technology monitoring such things as energy consumption and environmental quality. Though still testing the design, McCoy said the energy bill could potentially range between $30 and $40.
Another selling point was the quiet that permeates the home. Even though it parallels a busy street, the noise is immediately muted when standing inside. Terrell compared it to “living in a mini-bunker from World War I, but it’s modernized on the inside.”
Modeled to the millimeter, the house was designed by Ed Levy of architecture firm Cromwell. It was constructed on a property owned by Project:HOMES. RMT Construction & Development was the main contractor on the project. Alquist 3D, a 3D printing construction company, also was part of the group.
To get the development going, the team had to acquire a suitably sized 3D printer. Following an unsuccessful attempt to involve the Texas-based firm Icon, it paid $350,000 to purchase a BOD2 printer from Danish firm COBOD.
The gantry-system machine is 40-by-40-foot and directs a stream of concrete in a precise and predetermined line. Repetitively stacking such concrete strands on top of each other, a wall slowly emerges.
Arriving five months late, the printer’s first use proved to be a schooling exercise for those involved in the construction.
RMT’s Corey Todd and Tim Hill both described it as a fun experience, but remember a labor-intensive start. One issue that arose was the heat of Richmond summers.
The concrete’s dry time plays a pivotal role in determining how quickly to operate the machine: layer the material too soon and the wall will seep downward, layer it too late and the dry cement will not bond.
Although the printer’s program, Slicer, would suggest a speed at which to let out the cement, it was designed for Denmark’s climate and not Virginia temperatures, McCoy said. This could result in walls over three inches thick, an inch more than planned.
“We were still trying to figure out the machine, we were trying to get the right (concrete) consistency,” Hill said. “We built it and we had to tear it back down because it just didn’t look right. It wasn’t right, it wasn’t lined up correctly.”
At one point, someone broke in and stole the printer’s nozzle.
Instead of waiting for a replacement, a project technician used a desktop 3D printer to replicate the missing piece. There, the idea came up to add fins to the side, which ensured a consistent wall thickness moving forward.
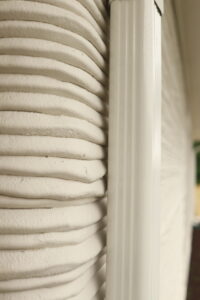
To construct the walls, the printer’s operators had to consider the heat and the speed at which to do it.
Such experimentation led to an improved process. The lessons learned were quickly applied to another house that was being printed in James City County, a project headed by Habitat for Humanity.
Hill described the second go-around as a much smoother experience that took less time and resulted in uniform walls. While the Richmond house took over two weeks to print, the second one was set up in a week and a half even with the same layout.
That project also saw a 60-65 percent reduction in the waste produced, McCoy said, in part thanks to the finned nozzle.
While the costs behind this venture are only now being analyzed, savings will become especially apparent when printing technology is used on a more massive scale.
“Scaling this up is critical,” McCoy added: “You’re not getting a lot of housing units for the current cost of using 3D printing.”
This may soon be the case, Virginia Housing Director of Strategic Housing Chris Thompson said. Alquist 3D has announced plans to print 200 homes.
New material considerations may also make the practice more affordable and sustainable, McCoy said. Already, his agency is working with the Department of Energy to try and use byproducts from coal firing and mining as alternatives to the cement content in concrete, which burns a lot of carbon when it’s made.
McCoy hopes to remove all concrete from 3D printing. He said it can use several other materials, such as polymers. His team is also starting to think about ways to use the technology for other parts of the building process beyond wall construction.
3D printing is not the only solution Virginia Housing has experimented with. Other ideas have included the conversion of shipping containers into homes and factory-manufactured houses.
Virginia Housing CEO Susan Dewey described an eager and excited response from the community, whether they were developers or nearby neighbors of the Carnation Street property. She said Terrell’s new home is only the beginning.
“This just shows what’s possible if we think outside the box a little bit,” Dewey said. “We have grants for partners that are looking at innovative ways to build homes, to finance homes.”

The 3D printed house at 217 Carnation St. has three bedrooms and two bathrooms in 1,550 square feet of space. (Filip De Mott photos)
A homebuilding experiment more than a year in the making helped first-time buyer Tiffany Terrell finally break through the competitive local housing market.
After a six-month search and a string of four failed bids, Terrell will soon close on a first-of-its-kind property in South Richmond: the region’s first 3D-printed house at 217 Carnation St.
With construction completed over a week ago and the deal set to close next month, Terrell, 38, will pay $235,000 to purchase the three-bedroom home from the project’s investment group, which includes local housing nonprofits Project:HOMES and Better Housing Coalition, along with Virginia Tech’s Virginia Center for Housing Research.
The idea to 3D print a house came about as a proof-of-concept in the ongoing effort to make living more affordable in the state.
Virginia Housing, formerly known as the Virginia Housing Development Authority, started looking into the practice in 2019. The group awarded a $500,000 grant to the Virginia Center for Housing Research, an organization that championed the embrace of technology as one viable solution to housing affordability.
“We did more studies of this house than you’ll ever see for a 1,550-square-foot house,” VCHR Director Andrew McCoy said. He added that the agency spent a lot of time focused on the energy efficiency of the space.
The recently completed structure, which includes two bathrooms and a sizable yard, now stands out from the rest of the street. A remnant of the building process, its outside surface is a stratified pattern of wavy cement.
The home is furnished with technology monitoring such things as energy consumption and environmental quality. Though still testing the design, McCoy said the energy bill could potentially range between $30 and $40.
Another selling point was the quiet that permeates the home. Even though it parallels a busy street, the noise is immediately muted when standing inside. Terrell compared it to “living in a mini-bunker from World War I, but it’s modernized on the inside.”
Modeled to the millimeter, the house was designed by Ed Levy of architecture firm Cromwell. It was constructed on a property owned by Project:HOMES. RMT Construction & Development was the main contractor on the project. Alquist 3D, a 3D printing construction company, also was part of the group.
To get the development going, the team had to acquire a suitably sized 3D printer. Following an unsuccessful attempt to involve the Texas-based firm Icon, it paid $350,000 to purchase a BOD2 printer from Danish firm COBOD.
The gantry-system machine is 40-by-40-foot and directs a stream of concrete in a precise and predetermined line. Repetitively stacking such concrete strands on top of each other, a wall slowly emerges.
Arriving five months late, the printer’s first use proved to be a schooling exercise for those involved in the construction.
RMT’s Corey Todd and Tim Hill both described it as a fun experience, but remember a labor-intensive start. One issue that arose was the heat of Richmond summers.
The concrete’s dry time plays a pivotal role in determining how quickly to operate the machine: layer the material too soon and the wall will seep downward, layer it too late and the dry cement will not bond.
Although the printer’s program, Slicer, would suggest a speed at which to let out the cement, it was designed for Denmark’s climate and not Virginia temperatures, McCoy said. This could result in walls over three inches thick, an inch more than planned.
“We were still trying to figure out the machine, we were trying to get the right (concrete) consistency,” Hill said. “We built it and we had to tear it back down because it just didn’t look right. It wasn’t right, it wasn’t lined up correctly.”
At one point, someone broke in and stole the printer’s nozzle.
Instead of waiting for a replacement, a project technician used a desktop 3D printer to replicate the missing piece. There, the idea came up to add fins to the side, which ensured a consistent wall thickness moving forward.
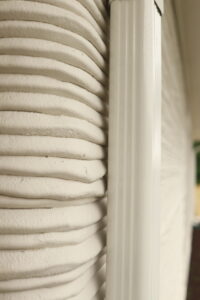
To construct the walls, the printer’s operators had to consider the heat and the speed at which to do it.
Such experimentation led to an improved process. The lessons learned were quickly applied to another house that was being printed in James City County, a project headed by Habitat for Humanity.
Hill described the second go-around as a much smoother experience that took less time and resulted in uniform walls. While the Richmond house took over two weeks to print, the second one was set up in a week and a half even with the same layout.
That project also saw a 60-65 percent reduction in the waste produced, McCoy said, in part thanks to the finned nozzle.
While the costs behind this venture are only now being analyzed, savings will become especially apparent when printing technology is used on a more massive scale.
“Scaling this up is critical,” McCoy added: “You’re not getting a lot of housing units for the current cost of using 3D printing.”
This may soon be the case, Virginia Housing Director of Strategic Housing Chris Thompson said. Alquist 3D has announced plans to print 200 homes.
New material considerations may also make the practice more affordable and sustainable, McCoy said. Already, his agency is working with the Department of Energy to try and use byproducts from coal firing and mining as alternatives to the cement content in concrete, which burns a lot of carbon when it’s made.
McCoy hopes to remove all concrete from 3D printing. He said it can use several other materials, such as polymers. His team is also starting to think about ways to use the technology for other parts of the building process beyond wall construction.
3D printing is not the only solution Virginia Housing has experimented with. Other ideas have included the conversion of shipping containers into homes and factory-manufactured houses.
Virginia Housing CEO Susan Dewey described an eager and excited response from the community, whether they were developers or nearby neighbors of the Carnation Street property. She said Terrell’s new home is only the beginning.
“This just shows what’s possible if we think outside the box a little bit,” Dewey said. “We have grants for partners that are looking at innovative ways to build homes, to finance homes.”
Its essential that we find new and more efficient ways to build affordable housing. Its at a crisis level. I’m very intrigued by this 3 D printing of houses instead of automatic weapons.
Well lets try testing a little more before we build with a new tool next time. That home in Southside took 14 months from clearance to sale so not really faster and it needed a $500k subsidy for a $235k home?? It will be interesting to see if any large builder will invest in this technology.
I am with you – I need more analytics before this thing is declared a “win”
I am shocked that it took 14 months to do one house made basically of cement. I am all for alternate affordable housing but over one year to deliver seems kind of meh… not impressed. I have seen many example where the delivery time was within 100 hours for the largest models so not sure why the time frame is what it is. Also for 235K I would not necessarily call that affordable. I always try to look at things on the positive side but to me this company definitely have their work cut out. With the price and the… Read more »
Not very familiar with how prototyping and grants work, are you? Usually testing of this nature results in big expenses with no post-testing payout. This project was able to recoup half the costs, while accumulating valuable lessons learned for continued development. I’d call that a win.
Do cement houses with 3″ thick walls last in the mid-atlantic? If so, why don’t we already have them using traditional cast methods? I understand the desire to use this new technology, but I would rather see private enterprise perfect the technique before using our tax dollars to build one house, rather than five, using traditional techniques.
In 1899 Thomas Edison founded the Edison Portland Cement Company. It constructed the world’s largest cement in New Jersey. Edison’s idea was mass producing inexpensive concrete houses. He patented a process for doing this. In addition, Edison wanted baths, toilets, sinks, cabinets —and even beds — to be concrete. Edison constructed a concrete cottage and a garage at his mansion in New Jersey. His grand idea, however, proved to be unworkable (the molds were too complex). I guess 3D printers are the solution.
PS: The Edison Portland Cement Company also constructed the original Yankee Stadium in The Bronx.
This is still very much at the proof of concept stage and the technology is improving all the time. A big part of that will be the ability to get away from concrete and towards more sustainable materials. We need to reduce our use of cement and making concrete houses is not good.
My own concern is the indoor environmental quality. Making houses out of impermeable materials needs serious mitigation to avoid mold and other moisture problems and suitable air changes to keep occupants healthy.
Interesting dilemma Garry. Wouldn’t this type of structure be similar to office buildings that have similar walls? At least this one has windows that can open The HVAC systems are indeed critical. And the energy savings has to account for something.